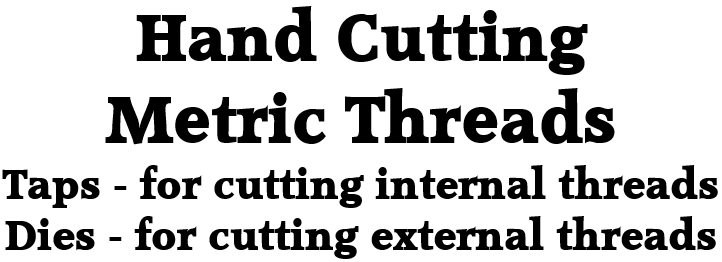
To cut an internal thread (cut a thread in a hole), you'll need a set of taps of the correct thread size and pitch. Usually metric taps are supplied as a set of three, designated taper, second and bottom. The picture shows a set of M12 x 1.75 taps. You should be able to see that the ends of the taps are slightly tapered. The most tapered one (far right) is unsurprisingly called the taper tap. The next (middle tap) is the second, and the last one is the bottom.
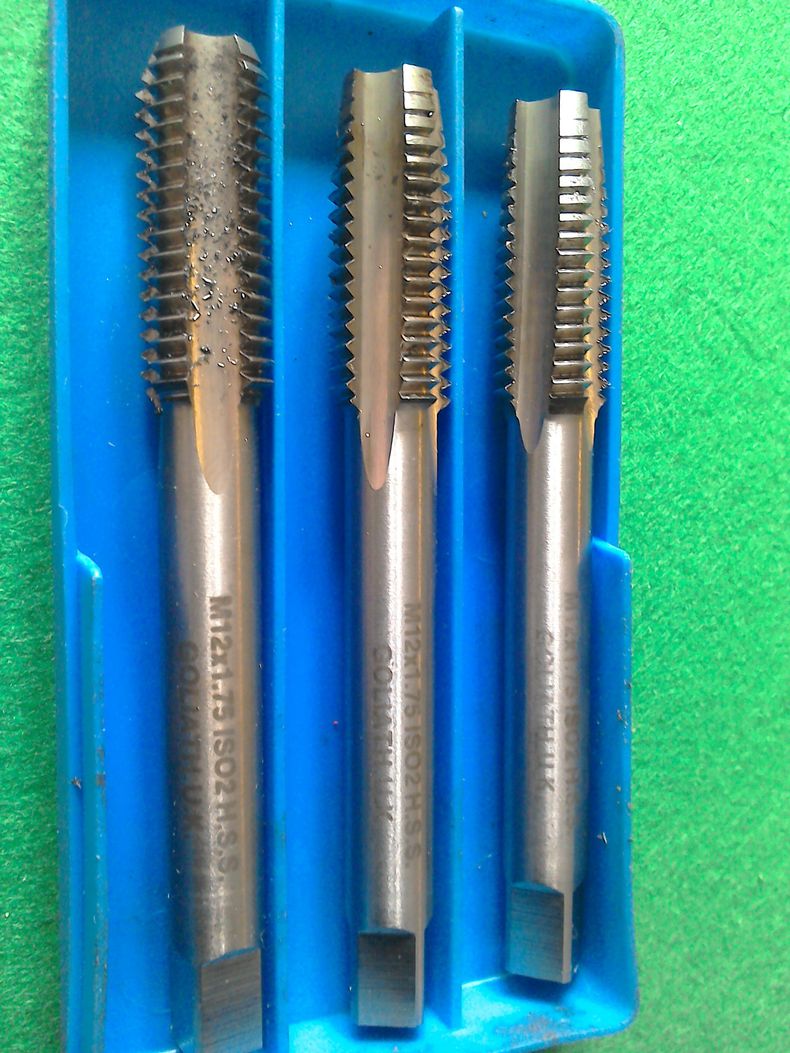
You'll also need a tap wrench to turn the tap. There are a couple of different designs, some examples are pictured below.
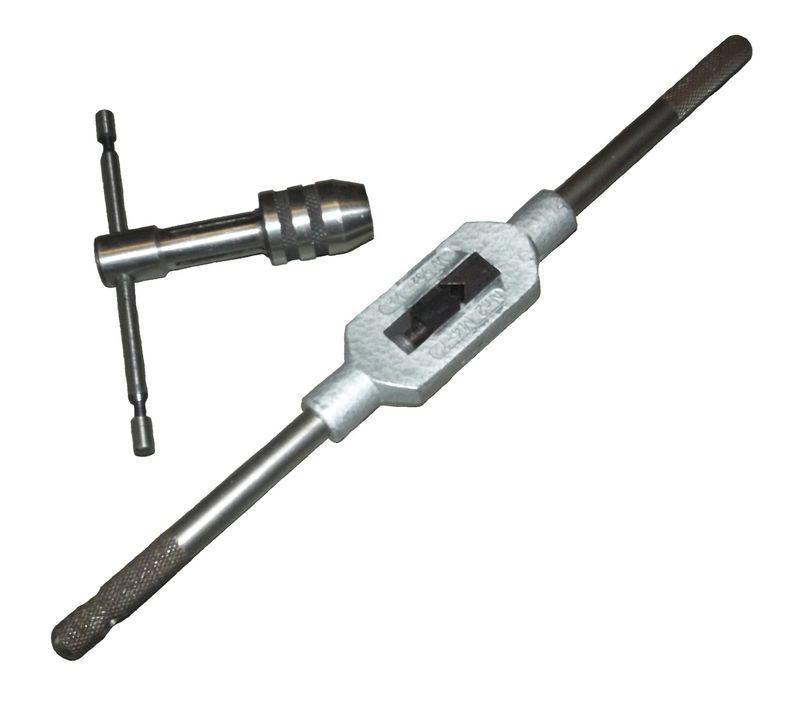
When tapping a blind hole, the hole needs to be drilled slightly deeper than the thread length required (typically one to two threads deeper). Start tapping with the taper tap. Ensure as you go that you are cutting square to the top surface of the work (check with an engineer’s square) and after every half turn, reverse direction to break up the chips. For a blind hole, occasionally remove the tap completely and clear the chips out of the hole. When the taper tap hits the bottom of the hole, repeat the procedure with the second and bottoming taps.
For through holes, you will probably only require the taper and second tap to finish the thread. The application of cutting fluid or paste will ease the process. Go carefully, breaking a tap off in your work creates a whole new world of grief!
Of course, before you can do any of that, you need to drill the correct size hole. The table below lists the most common metric thread sizes along with tapping drill size and clearance hole sizes. For example producing a threaded hole for an M10 x 1.5 bolt to screw in to would require a hole of 8.5mm diameter to be drilled and then tapped with the appropriate taps.
If the same bolt was required to pass through a hole, then a clearance drill of 10.2mm diameter would be used.
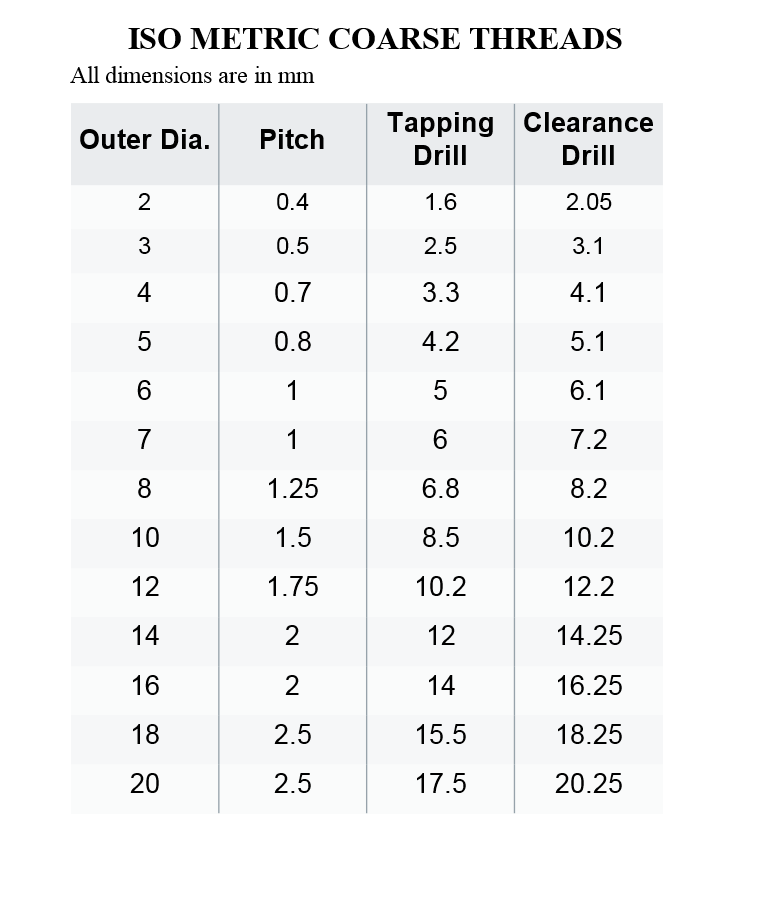
The action of using a die and diestock is similar to tapping, half a turn forward, reverse to break up the chips etc. It is also important to try and keep the die face square to the shaft.
If you are machining the shaft yourself, it is usual to machine the shaft slightly under the nominal size of the thread’s outer diameter (0.2mm undersize for threads M8 and above, 0.1mm or less for smaller threads). You can also slightly taper the end of the shaft. This will make it easier for the die to start cutting.
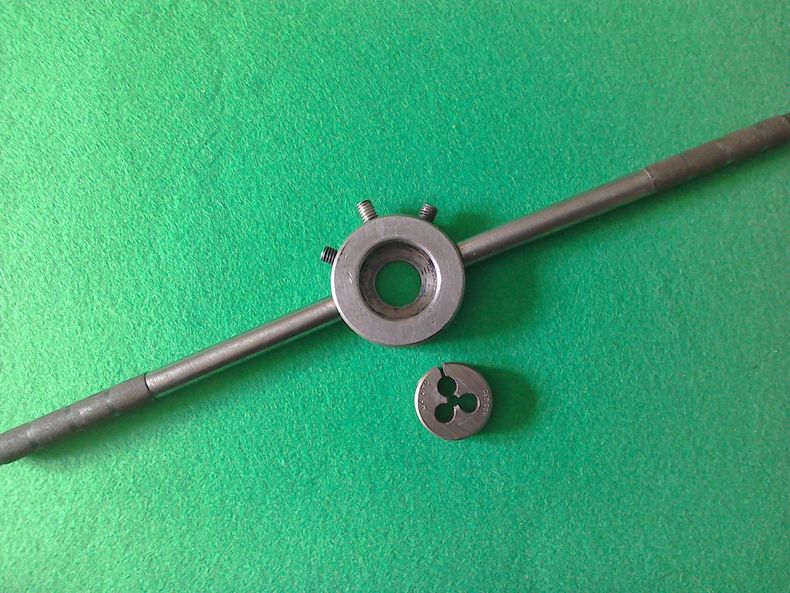
To cut external threads on shafts or bars by hand requires the use of a die and a die stock. The picture (below) shows a die and a distock. This is a split die, it can be opened or closed slightly by using the three screws on the diestock. Typically, on the first pass down the shaft, the centre screw is screwed in to open the die slightly. Release the pressure off the centre screw and tighten the outside screws slightly for the second pass to take a light finishing cut.
You may sometimes encounter a solid die, this should not be used for cutting a new thread, only for trying to repair a damaged existing thread. These are also available in a hexagon form and termed die nuts.
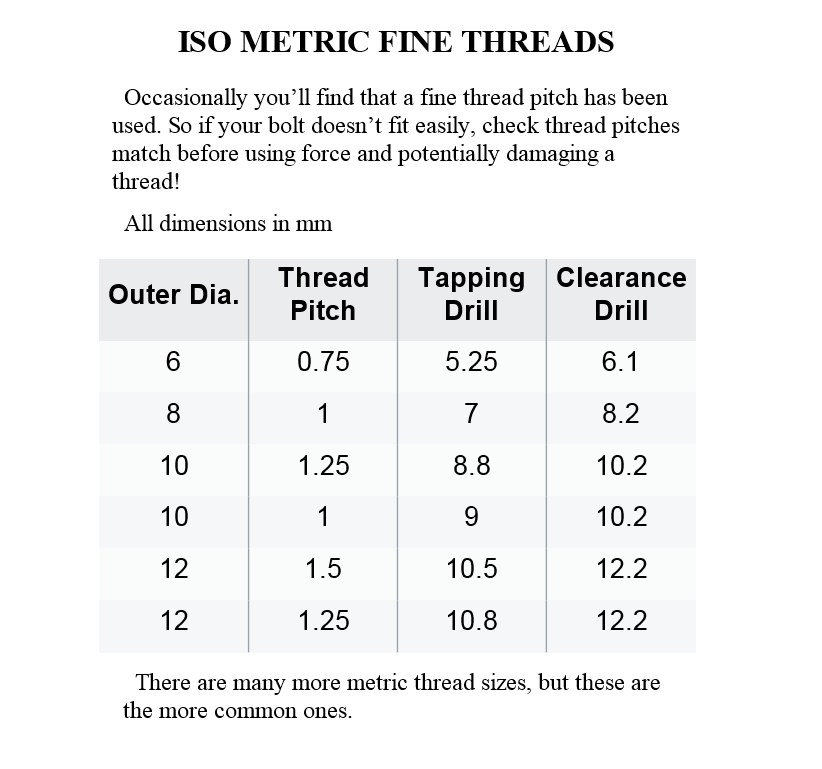