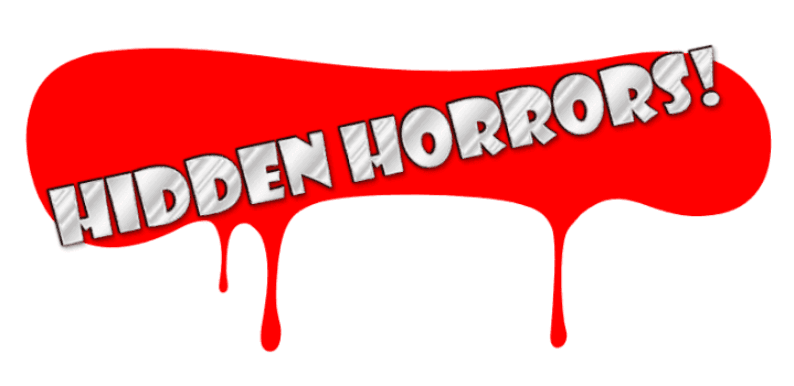
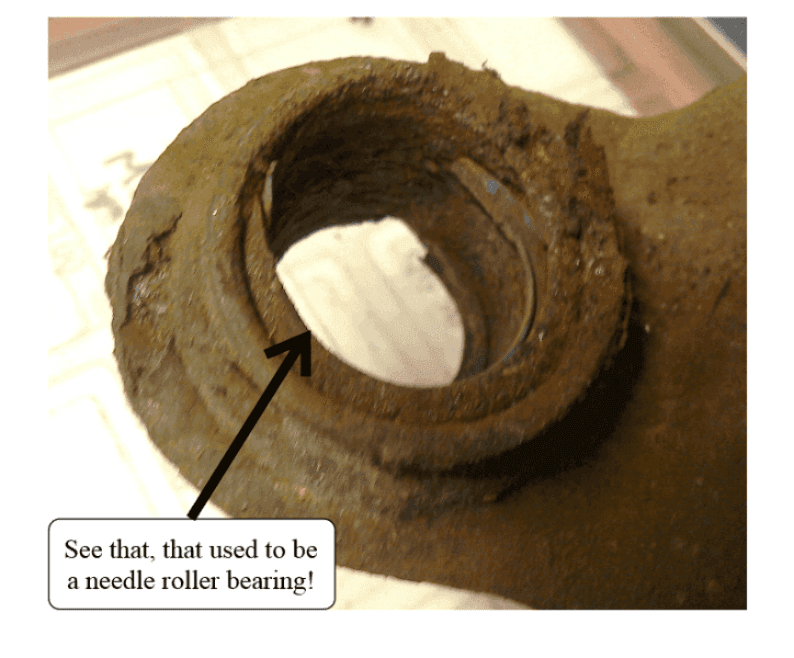
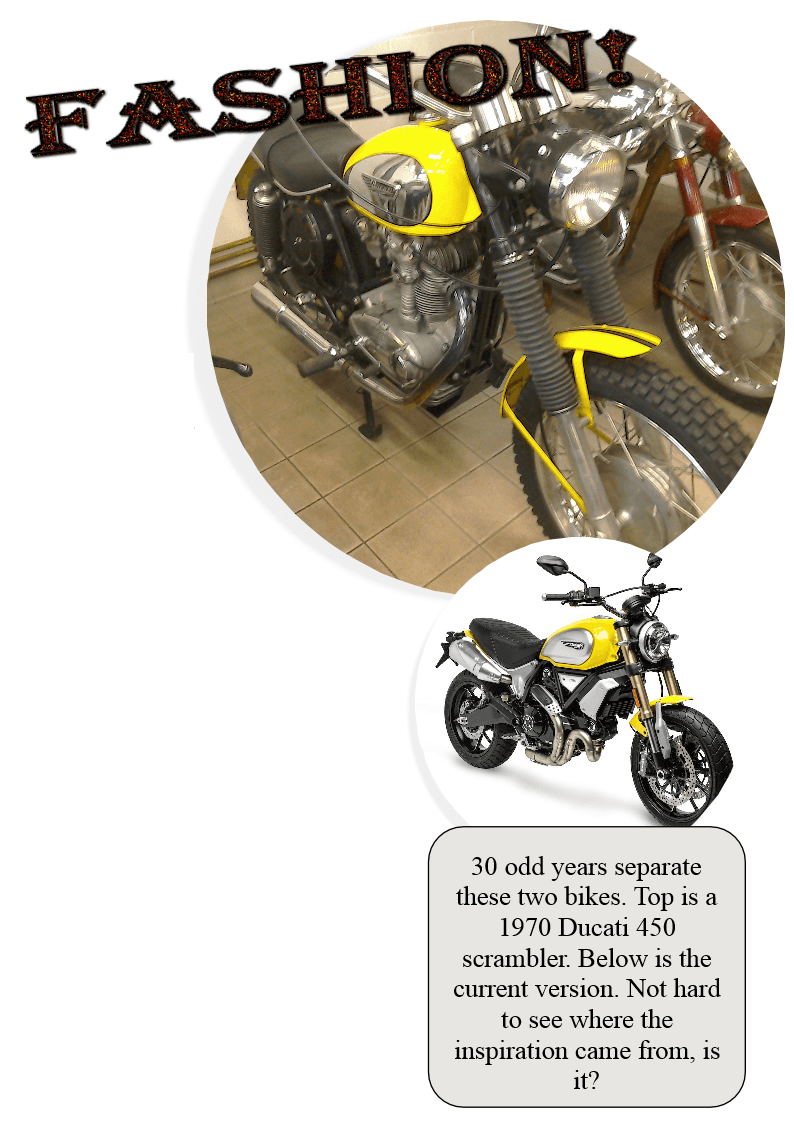
Ducati (like many Italian motorcycle manufacturers) has experienced fluctuating fortunes. It’s difficult to say which period was their golden years, but despite the 916 assisting Carl Fogarty’s rise to fame, it was the humble Monster that was the saviour of the modern Ducati factory and finally had their financial backers shouting, “let’s dance!” No matter which era of Ducati is your favourite, they are always a treat both in sound and vision and the new scrambler is certainly a hit with all the young dudes!
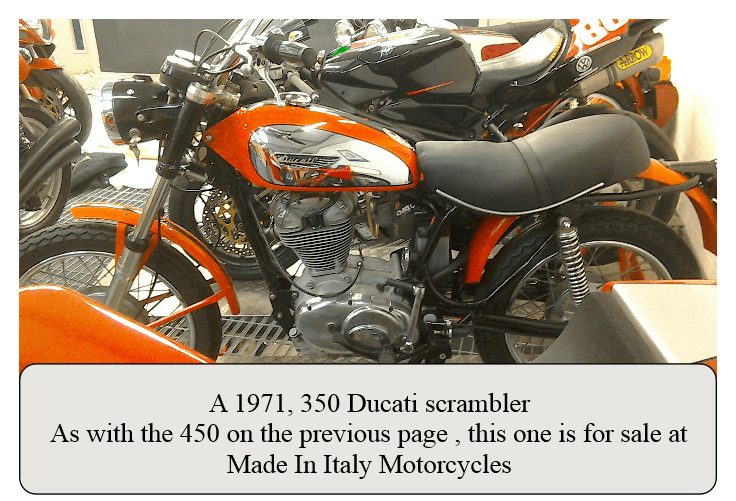
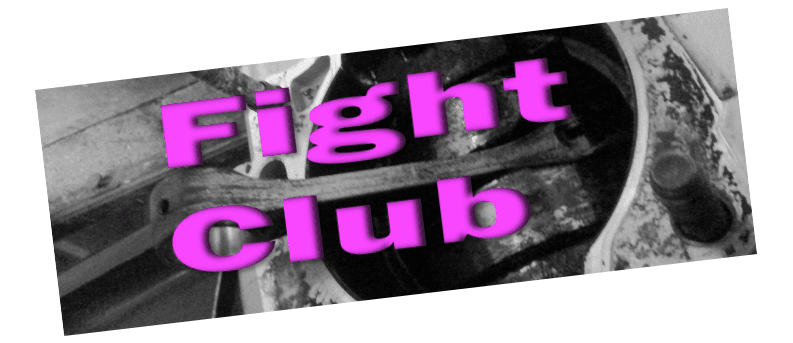
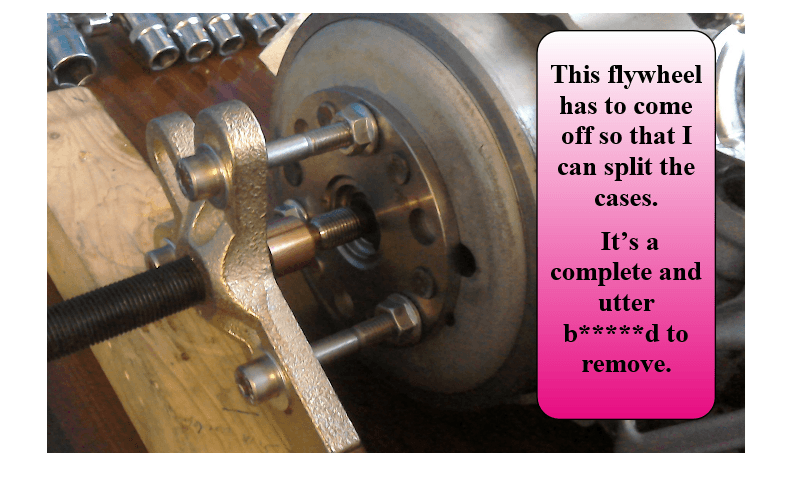
Now, it’s easy to say that the Toolzone puller was just cheap sh*t, but it was under serious strain when it gave way. Under more normal use, it may work just fine. Next up will be to see if the £18 bearing separator set that I purchased manages to pull the main bearing off the crank…
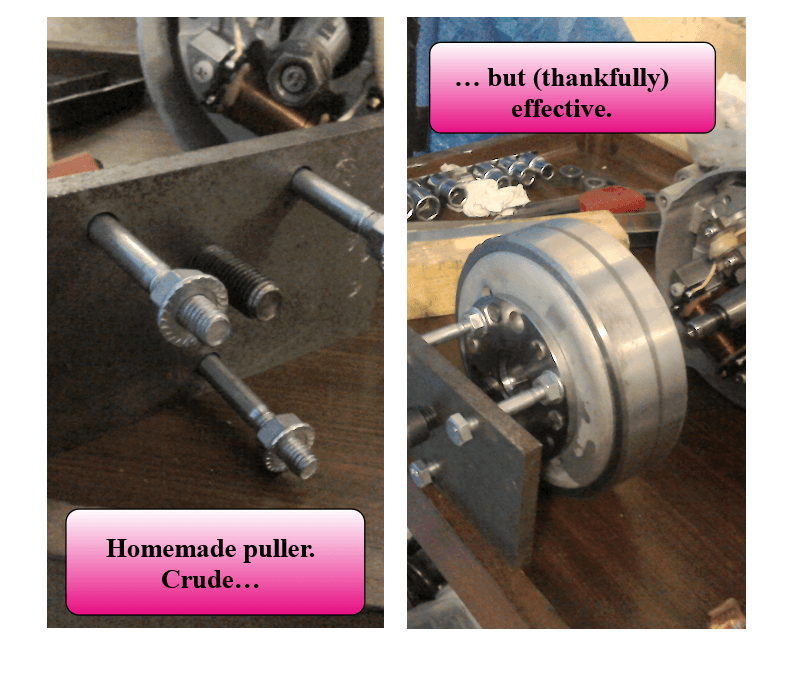
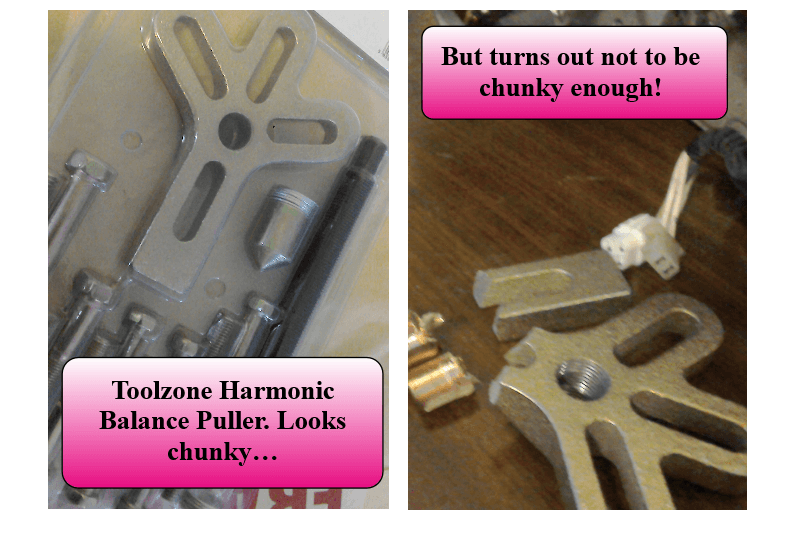
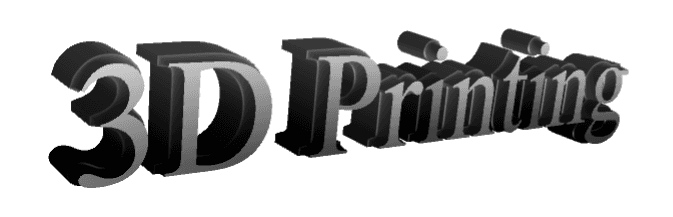
This Christmas, I managed to persuade my son that what he really wanted was a 3D printer. He’s into military history and recreating famous battles while playing miniature wargames. (Miniature wargames are basically posh boardgames, with tiny soldiers, tanks, vehicles etc. rather than boring old plastic counters.) He was sold when I showed him some of the models that other people had printed. It barely crossed my mind that it might possibly be of some use for the shed projects…
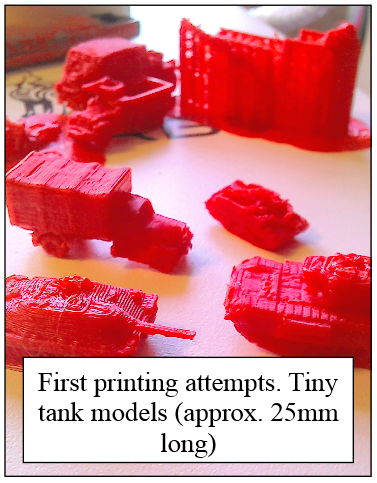
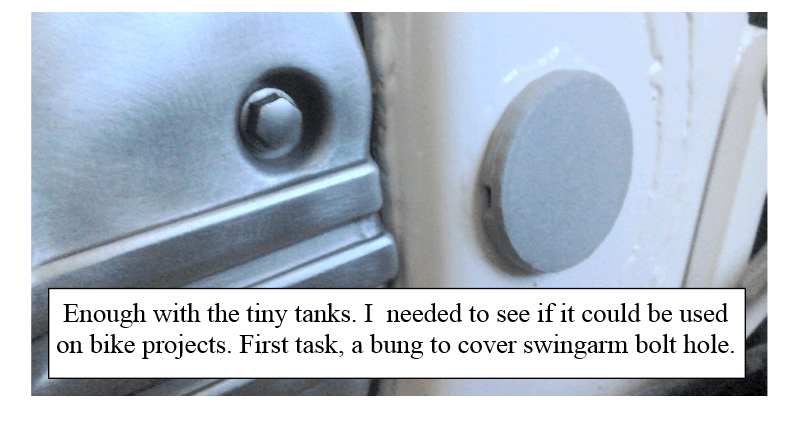
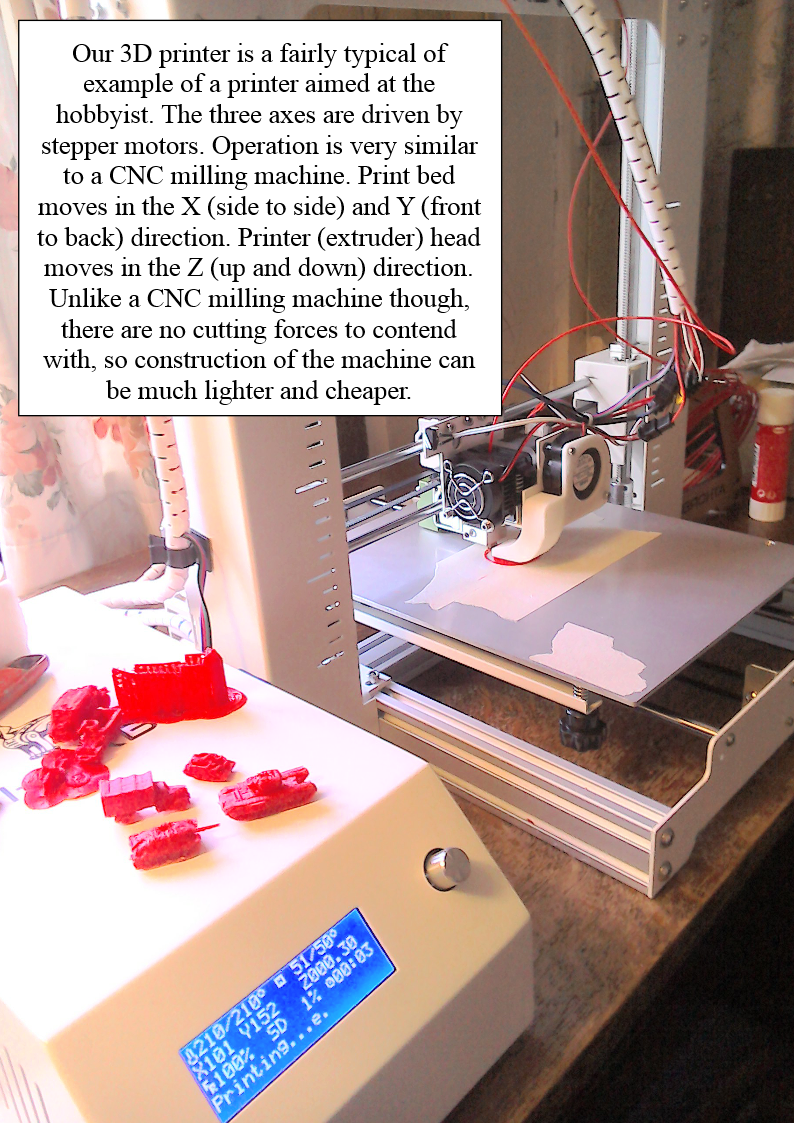
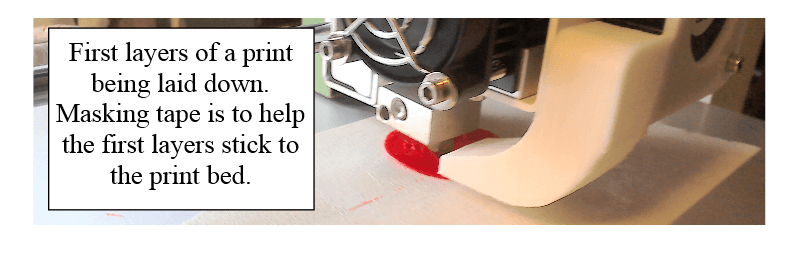
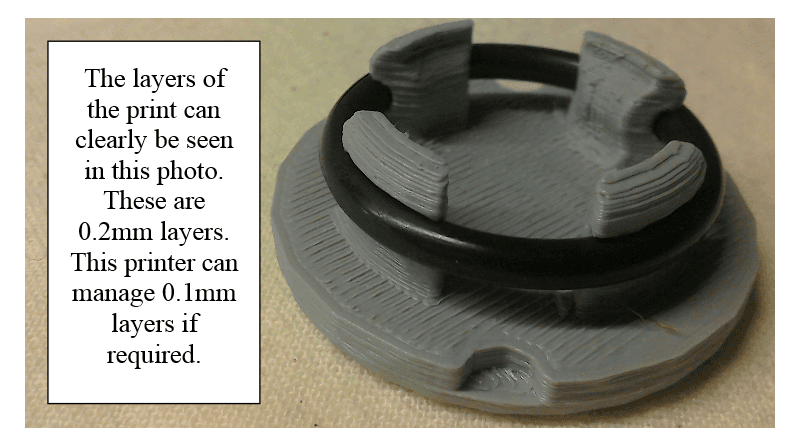
Pros…
Smaller and (possibly) cheaper and lighter than a lathe or milling machine. Great if you don’t have much space.
Although you shouldn’t leave it running unattended, you can be doing something else while you mind it.
You can produce shapes and features that would be difficult to machine conventionally.
Cons…
Steep learning curve. There are numerous settings and parameters which all have a bearing on the quality of your print.
Materials available for DIY use printers restrict it to non-structural parts.
If you want to make parts of your own design, you need to be able to access and use 3D CAD.