August 2018
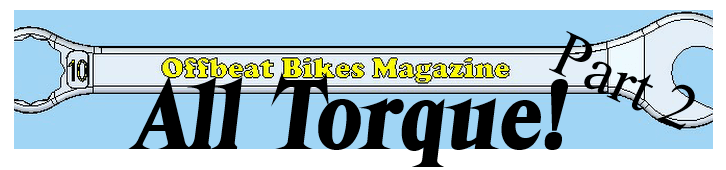
Is your torque wrench always by your side, ready to tighten every nut and bolt to the manufacturers specified value?
Or, does it lie in state in it’s protective case, only to see the light of day on special occasions? Perhaps you don’t own one at all.
I confess that mine only ever sees use when I’m working on an engine. Generally, for work on the bike’s chassis, it doesn’t get used. But here is part 2 of our discussion on making sure that your bolts are tight. You can make your own decision about when, where or how you use your own torque wrench.
Or, does it lie in state in it’s protective case, only to see the light of day on special occasions? Perhaps you don’t own one at all.
I confess that mine only ever sees use when I’m working on an engine. Generally, for work on the bike’s chassis, it doesn’t get used. But here is part 2 of our discussion on making sure that your bolts are tight. You can make your own decision about when, where or how you use your own torque wrench.
Ok, so last week we talked about how important it was for bolts to be correctly tightened. Then I left the cliffhanger ending, that maybe, even by using a torque wrench on every nut and bolt, you may still not be tightening your bolts to the required specification.
There are two forces at play when a bolt is tightened. The tension force initiated as the bolt begins to stretch (the bit that we want to happen) but also frictional forces caused by the contact between the male and female threads and the undersurface of the bolt head and the surface of the part as the bolt is turned. As a guide, about 80-90% of the torque applied using the wrench is used up overcoming these frictional forces. This is not a problem, since when the manufacturer sets the torque values, this frictional force is taken into account. The problem occurs when these frictional forces get modified. Hands up who puts a dab of grease or anti-seize on their fasteners. I know I do. Most of us have experience the pain of a bolt seized in place, and so we seek to minimise the chances of this happening again by a bit of lubrication. Unwittingly, we’ve just modified those frictional forces. In fact they’ve been reduced considerably. If the bolt is tightened to the same torque value as before, much less force is used up overcoming friction, and much more is available to stretch the bolt. This extra stretch means an over-tightened bolt, which in turn can cause stripped threads or damaged / broken bolts. Thread condition is vital. Unless specified otherwise, the torque value quoted by the manufacturer usually assumes a clean, dry thread.
Below is an example of torque settings from a Honda manual. Notice in the remarks column those bolts where threadlock or greases are to be applied. Otherwise, the threads are assumed to be clean and dry.
There are two forces at play when a bolt is tightened. The tension force initiated as the bolt begins to stretch (the bit that we want to happen) but also frictional forces caused by the contact between the male and female threads and the undersurface of the bolt head and the surface of the part as the bolt is turned. As a guide, about 80-90% of the torque applied using the wrench is used up overcoming these frictional forces. This is not a problem, since when the manufacturer sets the torque values, this frictional force is taken into account. The problem occurs when these frictional forces get modified. Hands up who puts a dab of grease or anti-seize on their fasteners. I know I do. Most of us have experience the pain of a bolt seized in place, and so we seek to minimise the chances of this happening again by a bit of lubrication. Unwittingly, we’ve just modified those frictional forces. In fact they’ve been reduced considerably. If the bolt is tightened to the same torque value as before, much less force is used up overcoming friction, and much more is available to stretch the bolt. This extra stretch means an over-tightened bolt, which in turn can cause stripped threads or damaged / broken bolts. Thread condition is vital. Unless specified otherwise, the torque value quoted by the manufacturer usually assumes a clean, dry thread.
Below is an example of torque settings from a Honda manual. Notice in the remarks column those bolts where threadlock or greases are to be applied. Otherwise, the threads are assumed to be clean and dry.
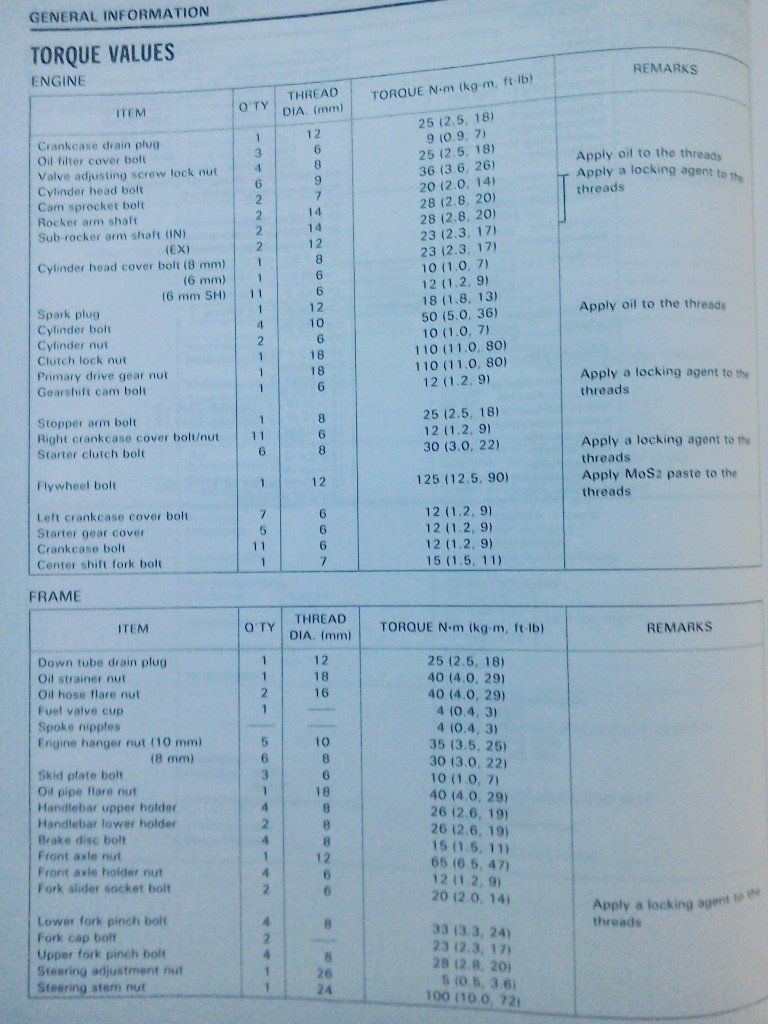
There are tables available giving ‘rule of thumb’ torque reduction factors for different types of lubrication. This one (below) is from ‘engineeringtoolbox.com’ There are others if you look.
So there you have it. Supplied torque values will only be accurate providing your bolt / thread / nut etc. is exactly as the manufacturer specified it. If you deviate from that, you need to be aware that the torque value may no longer be appropriate. So use your torque wrench with care!
So there you have it. Supplied torque values will only be accurate providing your bolt / thread / nut etc. is exactly as the manufacturer specified it. If you deviate from that, you need to be aware that the torque value may no longer be appropriate. So use your torque wrench with care!
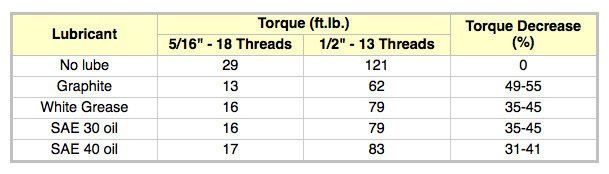
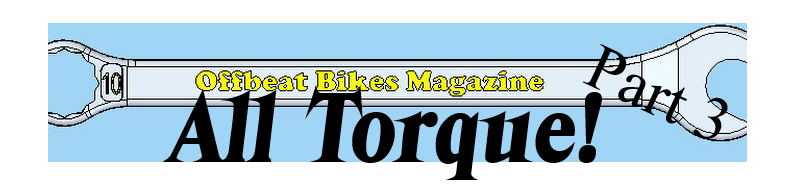
This week we’re going to have a very quick look at the units in which torque is measured, because they are many and varied. If you look at the extract from the Honda manual (shown above in part 2) you will see that they have quoted torque values in three different units; N.m (Newton meters), kg-m (kilogram meters) and ft-lb (foot-pounds).
I own three torque wrenches of different sizes. Their scales are variously marked as ftlbs and Nm, in-lbs (inch pounds) and m-kg, and Nm and mKg! Try not to get confused by the different way the units are written down, as there seems to be no consistent form. For example, FTLB, ftlb, ft.lb, ft-lb, ft-lbf, lbf-ft etc. are all the same thing and are more usually referred to as foot-pounds. Similarly, in metric units you might get kg-m, KGM, mkg, m.kg, kgf-m, m-kgf, again, they are all the same thing. The International Standard (S.I) unit of torque is the Nm or Newton meter and this is my preferred unit.
If you’re lucky, the units used in your workshop manual and those used on your torque wrench will be the same. Sometimes, they’re not and you’ll need to convert between units. Thankfully, nowadays, there are online calculators and apps that will do this for you.
Here’s one that covers most of the units that you’ll find.
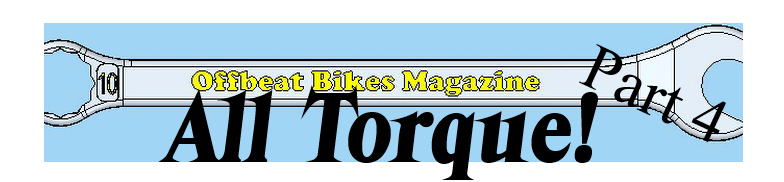
We’ve previously discussed a couple of things that affect whether our nuts and bolts are correctly tightened, such as thread lubrication and checking the correct units are being used, but you also need to be sure that your torque wrench is correctly calibrated. Most wrenches, even the cheap ones, usually come with a calibration certificate, so all should be pretty accurate when new. But, after some use and abuse, is it still reading true?
It is possible to get your wrench recalibrated, but at a price which isn’t going to appeal to a hobby mechanic. However, there are several youtube videos showing DIY methods of checking your torque wrench. I decided to check this one out:
So, armed with three pounds worth of digital luggage scale, I gave it a try myself. Well, let’s start off by saying that I don’t think that you can get really accurate results using this DIY method. There are too many areas where errors could creep in. Reading the scale at exactly the point that the wrench clicks is one. You also need to make sure that the load applied by the scale is acting exactly at the line marked on, and is always applied perpendicular to, the handle of the wrench. Repeating the exercise several times, and averaging the results achieved, eventually gave these figures.
For 1/4” wrench:
Setting Measured Value
4Nm 3.76Nm
14Nm 13.54Nm
24Nm 23.4Nm
For 3/8” drive wrench:-
Setting Measured Value
13.73Nm 15.81Nm
41.12Nm 40.22Nm
Setting Measured Value
13.73Nm 15.81Nm
41.12Nm 40.22Nm
For 1/2” drive wrench:-
Setting Measured Value
30Nm 31.78Nm
50Nm 49Nm
Given that the ISO (International Organisation for Standardisation) tolerance for torque wrenches is between +/- 4% and +/-6% depending on tool type and magnitude of applied torque, most of those measured values are actually Ok.
The 3/8” and 1/2” drive wrench were outside tolerance, but only on the lowest setting tested, with the 3/8” being the most inaccurate at over +15%. That one would obviously warrant further investigation. As it happens, I never use that particular torque wrench as I was never happy that it was accurate. It never quite felt ‘right’. Seems that I may have been justified in mistrusting it. But apart from that, it would seem that my torque wrenches are still OK for use.
One day, when I have a bit more time, I’ll try a greater range of settings
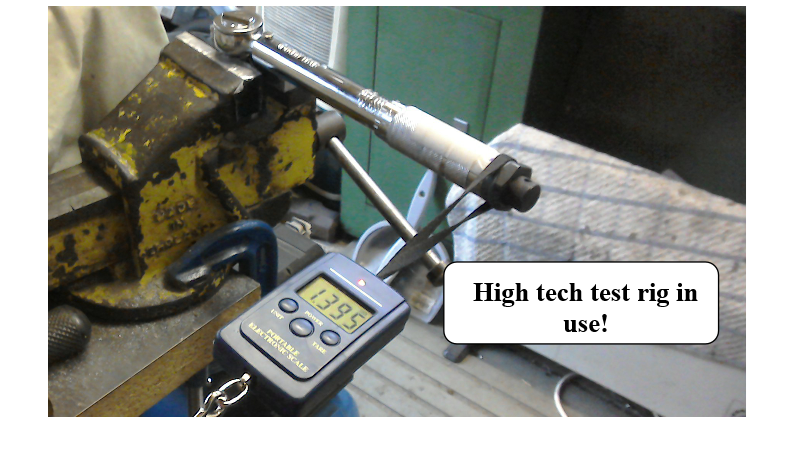