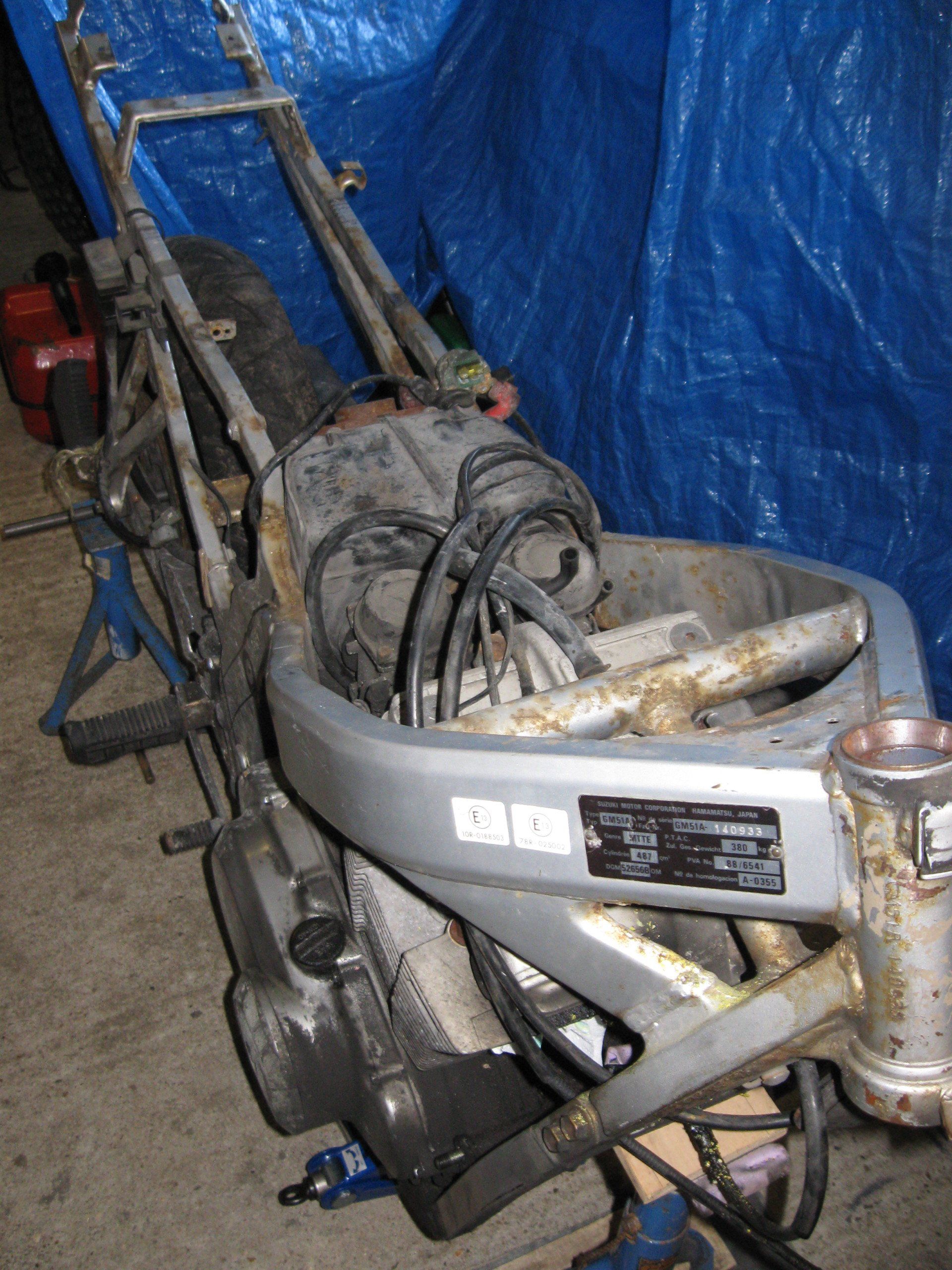
And so, the donor 'bike' arrives! Well at least parts of donor bike. The gearbox output shaft was worn, so the owner had decided to break the bike. All of the bodywork had been sold, but as I didn't want it, that was fine by me. I bought the rest of the bike for £130. The engine was supposed to be a good runner (although it had done 60,000 miles) but I had to take his word for it as so much of the electrical system had been removed that it wouldn't have been a quick job to see if it would fire up. I bought it on the basis that if nothing else, the engine would be fine to use as a mock up.
I'd forgotten just how filthy the engine was when it was purchased.
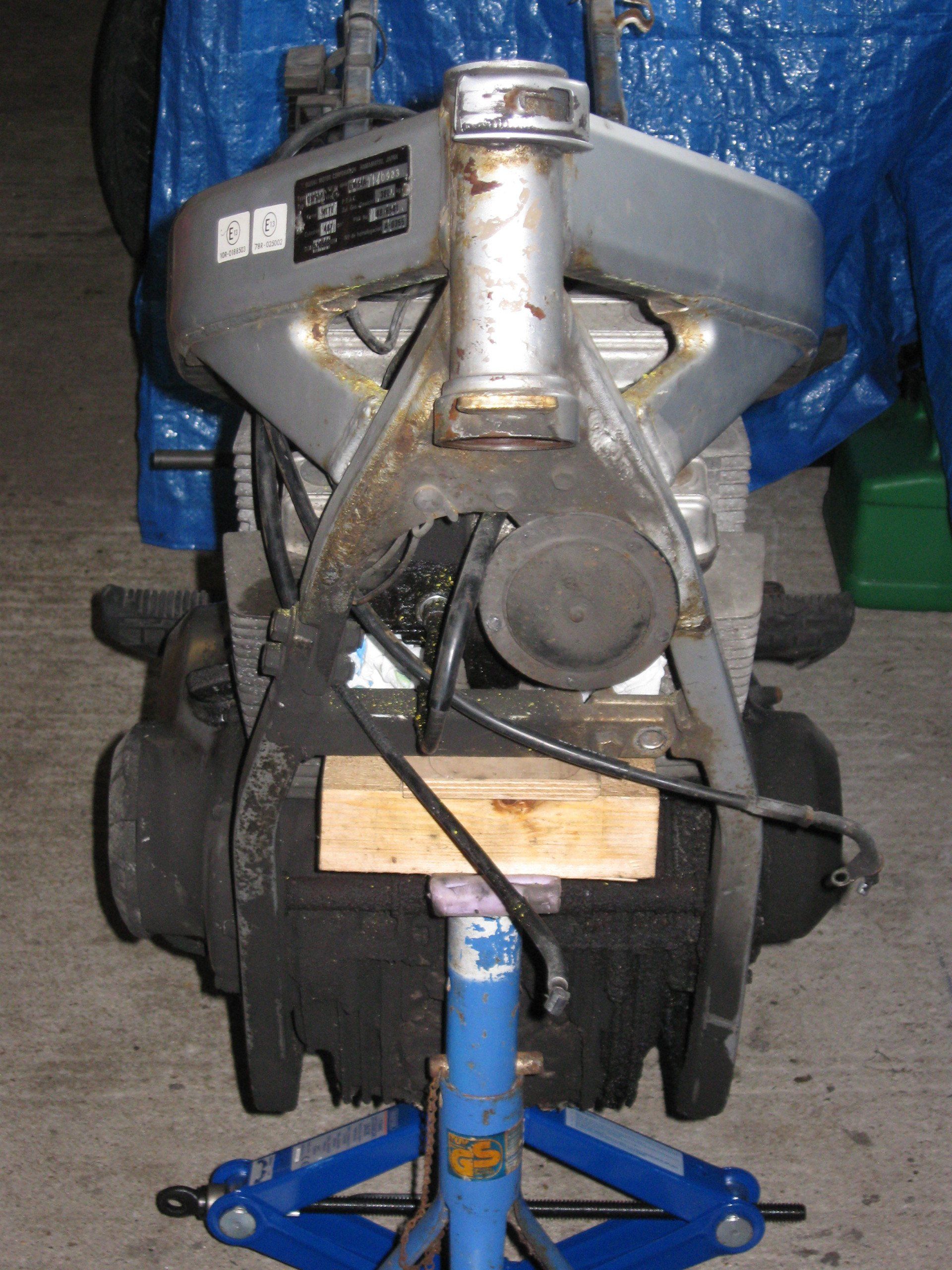
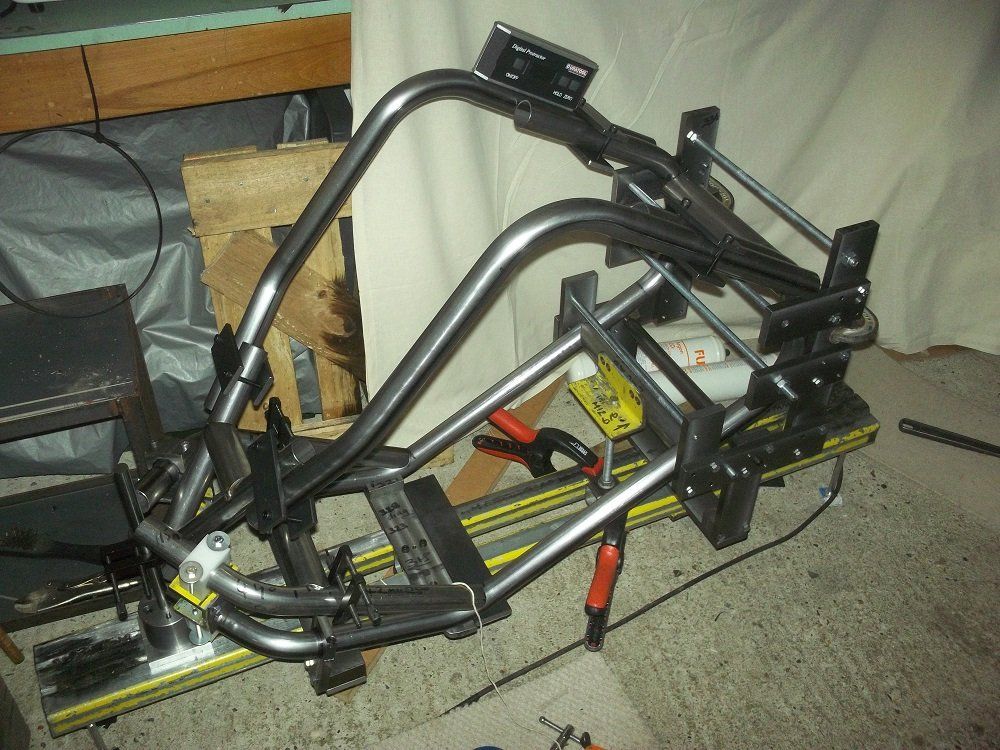
This is the frame jig that I built to use. I decided to build the frame upside down, so that the headstock could be fixed upright and directly to the jig. I hoped this would make it a simpler jig to build and make it easier to ensure that the headstock would remain perpendicular to the swingarm mountings. I'm not sure that it really made any difference, but I do know that it makes it difficult to visualise what the frame looks like when you're building it upside down. It also means that you can't trial fit the engine until the frame can be taken off the jig.
A closer look at the headstock end of the jig. All measurements for placing brackets, mountings etc. were taken from the centre of the headstock.
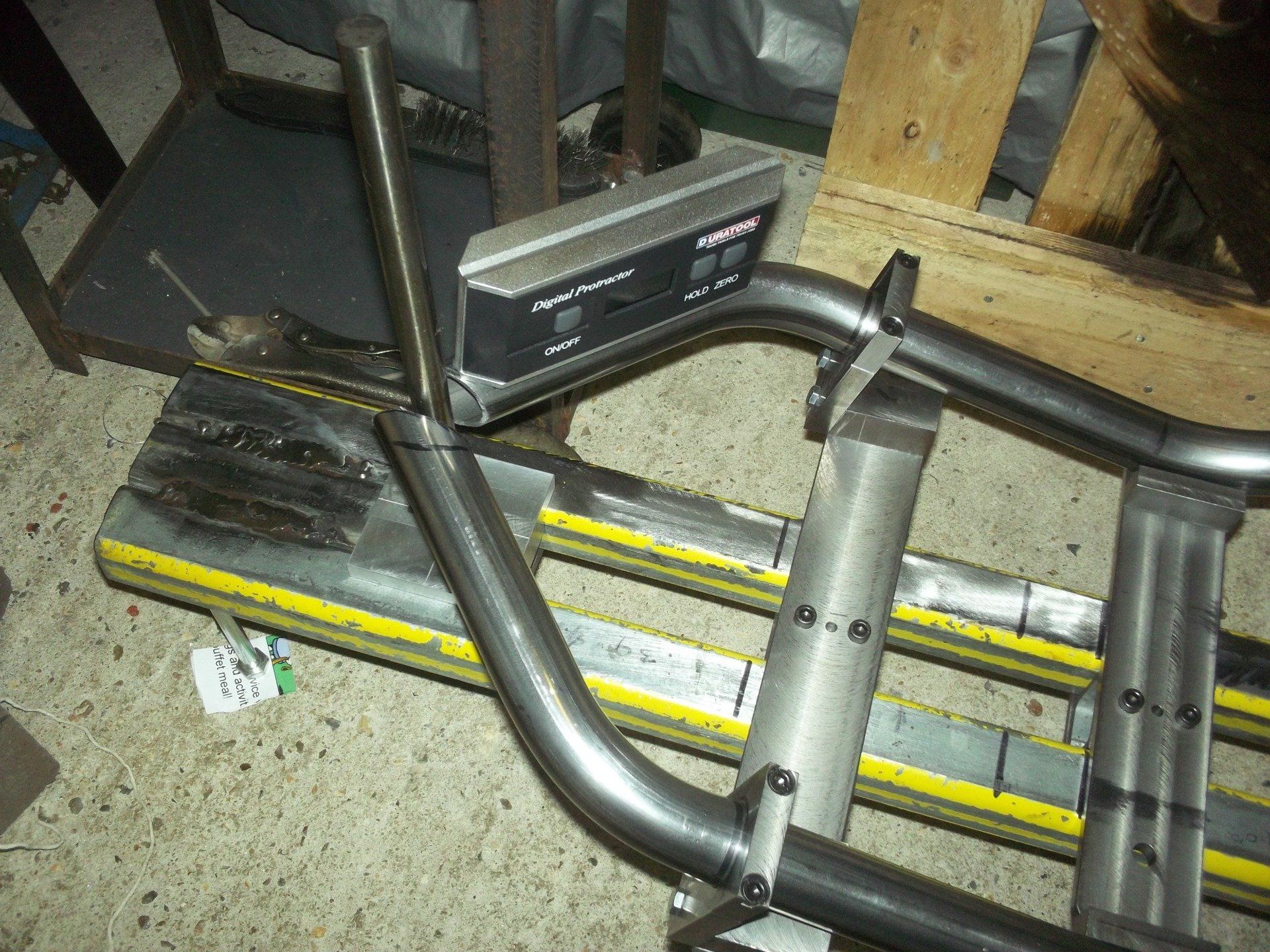
With the frame at last welded together and the engine in place, it was time to think about fuel tank and bodywork. I decided to make a box shaped petrol tank, that would be hidden by a fibreglass cover. The cover would also house the battery.
Here, the bodywork consists of foam, cardboard and paper! Patterns for the tank and tailpiece were made from foam sanded into shape, then coated in bodyfiller. Much sanding and filling is required to get a surface finish suitable for taking a mould from.
The first ever piece of fibreglass work that I made was the undertray / rear mudguard. The mould for this was made from mdf, foam and bodyfiller. I was incredibly relieved when the moulding released from the mould (and I still am relieved whenever a moulding successfully releases. My worst nightmare would be one sticking and ruining the mould).